Reducing cycle time is essential for improving efficiency, productivity, and overall performance in manufacturing. This blog post explores several key strategies to help you achieve this goal, focusing on automation, process optimization, and managing technical aspects effectively. And make sure you read to the end to find out how you can implement our production monitoring software and improve your cycle time absolutely free of cost!
What is Cycle TIme?
Cycle time is the total amount of time it takes to produce one unit, including preparation, idle time, and quality control checks. It is a great metric for manufacturers to track, as it shows how your production line is performing and whether strategies need to be put in place to improve efficiency. For a more in depth guide to cycle time and how to calculate it, check out our previous blog post.
Strategies To Reduce Cycle Time
Optimising cycle time so that you can produce more units in a smaller time frame is essential for increasing costs without having to increase input. As such, manufacturers need to find ways that they can reduce their cycle time, and here are 9 ways that you can do just that.
Streamline the Process
Streamlining the manufacturing process is essential for reducing cycle time and enhancing efficiency. This involves critically assessing and revising the sequence of operations to eliminate unnecessary steps and simplify tasks. By removing redundancies and activities that do not add value, workflows can be made more efficient. For example, a manufacturer might streamline their assembly line by combining inspection and packaging steps, reducing the time each unit spends in production and quickly moving products to shipment, thereby significantly cutting down cycle times.
Optimise Workflows
Balancing workloads and standardising operations are critical for optimising production workflows. Ensuring that work is evenly distributed among workers and machines prevents bottlenecks and reduces idle time. For example, relying on only one or two individuals for a specific task is risky as it can lead to delays if they are unavailable or overworked. By spreading the workload and implementing standard procedures for everyone to follow, production cycles become more predictable and efficient.
Implement Lean Manufacturing Techniques
Adopting lean manufacturing techniques such as the 5S methodology (Sort, Set in order, Shine, Standardise, Sustain) and Kaizen (continuous improvement) can dramatically improve production efficiency. These methodologies focus on organising the workplace and promoting ongoing incremental improvements by involving employees at all levels. This participatory approach can lead to significant reductions in cycle time by continuously identifying and eliminating waste. Additionally, lean techniques help foster a culture of continuous improvement, which is essential for long-term efficiency gains.
Reduce Setup and Changeover Times
Minimising setup and changeover times is essential for reducing cycle time. Techniques like Single-Minute Exchange of Die (SMED) can streamline the changeover process, drastically cutting down the time needed for equipment setup. This allows for quicker transitions between production runs and increases overall equipment availability and efficiency. By reducing the non-productive time during changeovers, manufacturers can keep production lines running smoothly and reduce delays.
Automate Processes
Implementing automation through robotic process automation (RPA), artificial intelligence (AI), and modern machinery can accelerate repetitive tasks and reduce the likelihood of human error. Upgrading to faster, more efficient equipment can also increase production speed, allowing for more units to be produced in less time without sacrificing quality. Similarly, automation helps in maintaining consistent output, where each unit is produced is the exact same time. You cannot get this level of efficiency with humans, and it also means employees are free to focus on more complex and value-added tasks.
Enhance Quality Control
Improving quality control measures by implementing real-time monitoring and statistical process control can help detect and address production anomalies quickly. This proactive approach minimises the need for rework and scrap, therefore reducing cycle time and enhancing overall efficiency. Advanced quality control systems can provide immediate feedback, allowing for rapid corrections and maintaining high standards throughout the production process. Busroot, our production monitoring software, will help you do this by tracking all causes of quality issues and sending automatic alerts whenever something happens. It provides you with real-time insights into the key issues and this information can then be used to put mitigation in place, which can significantly improve cycle time!
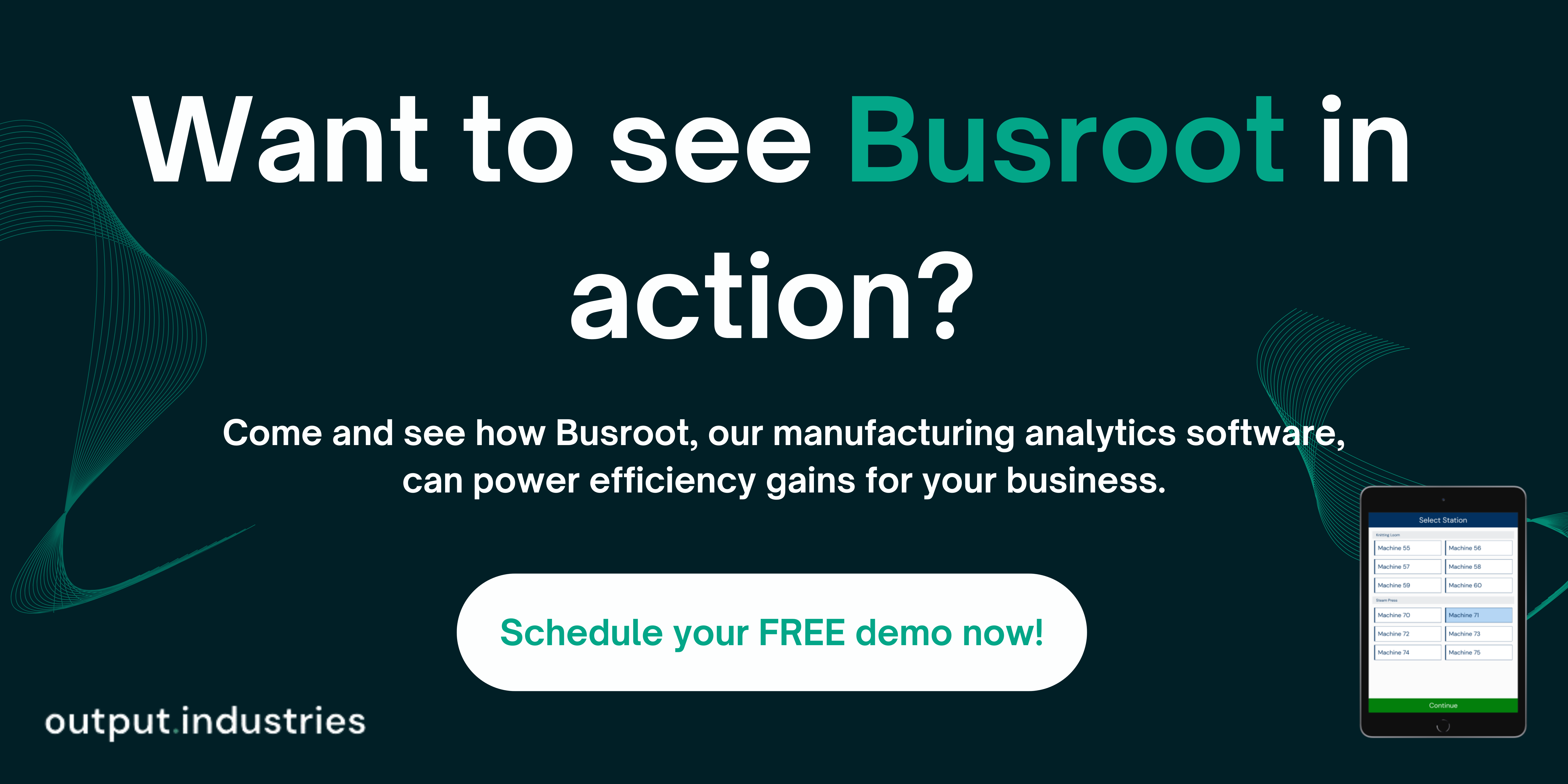
Improve Supply Chain Management
Optimising supply chain management through strategies like Just-in-Time (JIT) inventory can reduce both inventory costs and production delays. Strengthening relationships with suppliers ensures that materials are delivered as needed, preventing production interruptions and supporting a smoother manufacturing process. Efficient supply chain management helps in maintaining a steady flow of materials, aligning production schedules closely with demand, and reducing the waiting time for raw materials and components.
Employee Training and Involvement
Regular training and the continuous development of employee skills ensure that workers are efficient and versatile. Empowering employees by involving them in decision-making and problem-solving processes can motivate them to identify and implement improvements in the production process. Well-trained employees can adapt more quickly to new processes and technologies, contributing to shorter cycle times. Encouraging a culture of continuous learning and involvement helps in maintaining high productivity and efficiency levels.
Monitor and Analyse Performance
Consistently tracking cycle times and other relevant metrics, such as OEE and machine downtime, using Key Performance Indicators (KPIs) is crucial for identifying improvement opportunities. Without KPIs, you won't be able to see where the business is at, and whether it is making progress. As such, establishing feedback loops to collect insights from all stakeholders—workers, managers, and suppliers— is essential for monitoring progress and continual refinement of processes. This regular analysis of performance data helps in pinpointing bottlenecks and inefficiencies, enabling targeted improvements. By monitoring and analysing performance consistently, manufacturers can make informed decisions that drive down cycle times and enhance overall productivity.
These strategies collectively improve efficiency, reduce delays, and enhance overall productivity, positioning manufacturers to meet market demands more effectively.
Implement real-time production monitoring for FREE!
Thanks to innovative funding from MakeUK, our Lighthouse project is offering 25 manufacturers that chance to implement Busroot completely free of cost. You will benefit from the valuable insights on OEE, machine downtime, cycle time, asset utilisation, quality and more. Some of our customers have seen an increase in output of 15% just 2 months after implementing Busroot, so you don't want to miss out! Check out our Lighthouse Project page for more information, or contact us now to schedule a demo.