One of the key issues that manufacturers constantly face is the reduction and elimination of waste. Unnecessary waste is a massive money drain, and can cause companies to go out of business if not addressed quickly. This blog will go through the principles of lean manufacturing, the 6 big losses, and how to avoid them.
What is Lean Manufacturing?
Lean manufacturing is a systematic method focused on reducing waste while increasing productivity. It involves continuous efforts to achieve stable and predictable process results by identifying inefficiencies and putting in place mitigation. Embracing lean principles is vital for manufacturers looking to improve their processes and reduce unnecessary costs.
Lean manufacturing is centred around five key principles that drive all decision making. These principles are as follows:
- Define Value: The first principle of lean manufacturing involves defining value from the customer's perspective and creating products that meet or exceed customer expectations. This value could be in the quality, functionality or price.
- Map the Value Stream: Once value is defined, the next step is to map the value stream. This involves identifying every step in the process chain, from raw materials to customer delivery, and documenting the information and material flows required to bring a product or service to the consumer. Mapping the value stream helps identify and eliminate waste.
- Create Flow: After removing the wastes identified in the value stream mapping, the next principle focuses on making the value-creating steps occur in a tight sequence so the product will flow smoothly towards the customer.
- Establish Pull: The pull system is about ensuring that nothing is made ahead of time, building inventory only when there is demand from the customer. This strategy helps avoid overproduction—one of the most critical forms of waste in lean manufacturing.
- Pursue Perfection: The final principle of lean manufacturing is the pursuit of perfection through continuous improvement. This involves continually looking for ways to increase efficiency and eliminate waste in the value stream.
By addressing each principle, manufacturers can make sure they are assessing their entire production flow, and reducing inefficiencies wherever possible.
The Six Big Losses
The six big losses in manufacturing are critical areas where inefficiency can creep into production, potentially leading to increased costs and reduced throughput. Tackling these losses is crucial for maintaining competitive advantage and achieving high levels of customer satisfaction. Addressing these losses also directly contributes to enhancing overall equipment effectiveness (OEE), which is a measure of manufacturing productivity. We will now describe each of the 6 big losses and how you can avoid them.
Unplanned Stops/Downtime
Unplanned stops are sudden halts in production due to equipment failures or breakdowns. They are the most critical because they result in immediate and often substantial production delays. Unplanned stops are usually caused by machine failure, stock/inventory issues and operator error.
There are several ways in which you can reduce the frequency of unplanned stops, including:
- Preventive Maintenance: Implement a regular maintenance schedule for all equipment to catch and address potential failures before they lead to unplanned stops. This can include routine inspections, oil changes, and parts replacement at prescribed intervals.
- Predictive Maintenance: Utilise advanced technologies such as IoT sensors and AI to monitor equipment conditions in real-time. This allows for the prediction of equipment failures before they occur, enabling proactive maintenance and repairs.
- Training Operators: Ensure that all operators are well-trained on the equipment they use. Knowledgeable operators can identify signs of potential problems early, reducing the likelihood of major breakdowns.
Planned Stops/Downtime
Planned stops, while necessary for tasks such as equipment servicing or adjustments for new product runs, still halt production. If not optimised, they can significantly reduce productivity and impact profit margins. Check out our blog to understand the true costs of downtime.
Ways in which you can reduce planned stops include:
- Optimising Setup and Changeovers: Streamline setup and changeover processes by using techniques like SMED (Single-Minute Exchange of Die). This method aims to reduce the time it takes to switch from running one product to another to under 10 minutes.
- Schedule During Low Demand: Plan for maintenance and changeovers during periods of low demand whenever possible. This strategy minimises the impact of downtime on overall production output.
- Standardisation of Work: Develop standard operating procedures for changeovers and maintenance. This reduces variability in how tasks are performed and speeds up both processes.
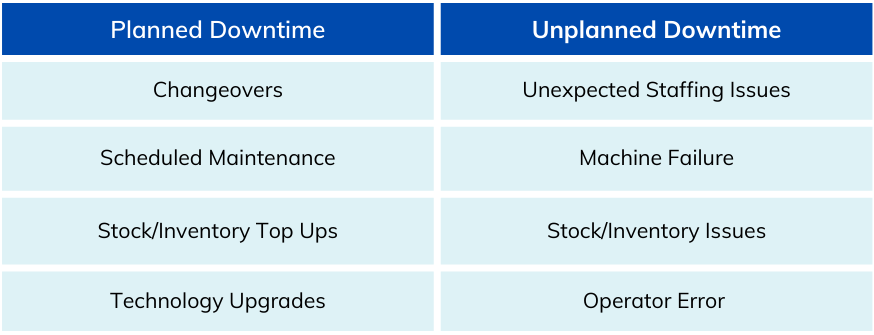
Small Stops
Small stops occur when machinery halts temporarily and briefly, often caused by minor equipment malfunctions or component misfeeds. Although each stop is short, their cumulative effect can be significant. Solutions include:
- Equipment Fine-tuning: Regularly adjust and calibrate machines to prevent frequent minor stops caused by misfeeds, sensor blockages, or small jams.
- Improve Material Handling: Enhance the reliability of material feeds to the production line. Use quality materials and ensure they are handled properly to avoid misalignment or blockages that can cause brief stops.
- Employee Empowerment: Train and empower employees to make minor adjustments and fixes without waiting for specialised maintenance teams. This reduces downtime dramatically.
Slow Cycles
Slow cycles are instances when equipment operates at speeds slower than its optimal capacity. Causes can include suboptimal machine settings, operator errors, or wear and tear on machinery. This is an issue because it reduces the quantity of units that you can produce in a shift, reducing your overall productivity and profitability.
Ways to reduce slow cycles include:
- Regular Calibration: Maintain equipment to operate at optimal speeds. Regular calibration ensures that machinery operates as efficiently as possible.
- Upgrade Equipment: Invest in newer, more efficient technology that can operate at faster speeds and with greater precision.
- Operator Training: Continuously train operators to ensure they are using equipment in the most efficient way, adhering to best practices for operation and monitoring.
Production Rejects
Production rejects are products that fail to meet quality standards, and this can happen at any point throughout the production cycle. These rejects represent a direct loss of materials and time. This can be caused by material blockages, operator error or machine malfunction. Production rejects can be reduced by:
- Quality Control Systems: Implement rigorous quality control systems throughout the production process. Use automated inspection systems where possible to detect and correct defects early in the production process.
- Feedback Loops: Create quick feedback loops to inform operators and supervisors of defects. Prompt responses can prevent further rejects.
Startup Rejects
Startup rejects occur at the beginning of production runs or after setup changes, where the process may not yet be stabilised. As a result the units may not be the correct shape or the wrong colour etc. These rejects can be due to a number of reasons, such as improper machine setup, operator errors and the need for equipment to reach certain operational conditions, such as temperature and pressure.
Minimising these rejects involves:
- Soft Start Procedures: Develop procedures for a gradual start to production to ensure everything is working correctly before full-scale production begins.
- Pre-Start Checks: Implement comprehensive pre-start checks and trial runs after any significant changeover or maintenance activity. This helps identify any issues that could cause rejects when production ramps up.
- Training and Standardization: Standardise startup procedures and ensure all staff are trained on them. This reduces variability and the risk of errors leading to defects.
Implementing Technologies to Reduce Big Losses
One of the most efficient ways to reduce losses is to implement an advanced manufacturing analytics software. These can identify and alert you of downtime, quickly identify inefficiencies, and implement predictive maintenance schedules. Busroot has helped many companies improve their downtime and increase revenue, thanks to its insights and analysis of key performance metrics like OEE and cycle time.
Busroot helped A1 Bacon to increase their production output by 14% in only 2 months! If you’d like to experience some of these gains for yourself, get in touch and we can schedule your free demo!
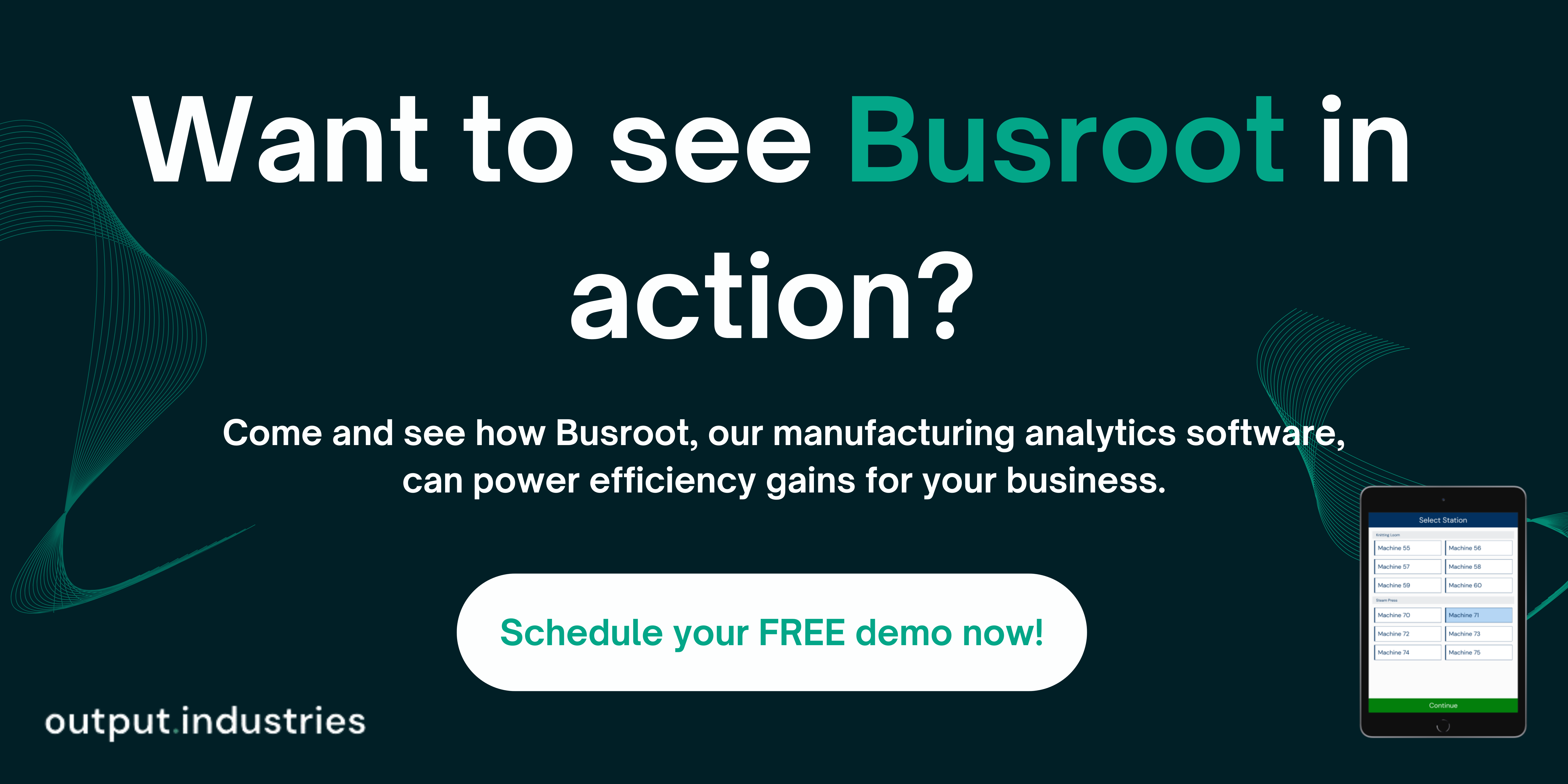