Production line efficiency is a critical metric for manufacturers aiming to maximise output while minimising waste and operational costs. Understanding and optimising this efficiency can lead to significant improvements in productivity, profitability, and competitiveness. Efficient production lines are streamlined, less prone to errors, and operate with minimal downtime, making them key to achieving sustainable manufacturing goals.
What is Production Line Efficiency?
Production line efficiency evaluates the ratio of actual output to the maximum possible output within a given time frame, expressed as a percentage. This measure provides crucial insights into the effectiveness of a production line in utilising resources and achieving its full potential. "Production line" can refer to one machine, or the entire production process. You can measure it however is best for the organisation.
High efficiency indicates optimal use of materials and labour, where the production line outputs close to what is theoretically possible without wastage or delay. On the other hand, low efficiency can highlight problems such as equipment malfunctions, suboptimal processes, or workforce inefficiencies.
Importance of Measuring Efficiency
Measuring production line efficiency is incredibly important if you want to maximise profits and improve productivity. Some of the reasons why include:
- Cost Reduction: By understanding how efficiently a production line operates, a company can identify areas where resources such as materials and energy are being wasted. Addressing these inefficiencies helps reduce production costs, which can lead to lower overall operating expenses and increased profitability.
- Productivity Improvement: Efficiency metrics help pinpoint where production bottlenecks and slowdowns occur. By resolving these issues, companies can increase the throughput of their production lines, thereby boosting overall productivity. This is particularly vital in high-demand scenarios where meeting production targets is essential to fulfilling customer orders on time.
- Quality Control: There is often a direct correlation between the efficiency of a production line and the quality of the output. Inefficient processes can lead to rushed or incomplete assembly, machine overuse, and operator errors, all of which can compromise product quality. Regular monitoring of efficiency helps ensure that products meet quality standards consistently.
- Maintenance and Upgrades: Efficiency measurements can signal when machines are underperforming or failing, which might indicate a need for maintenance or replacement. Proactive maintenance based on efficiency metrics can prevent costly downtime and extend the lifespan of machinery.
- Capacity Planning: Understanding the efficiency of production lines enables businesses to make informed decisions about capacity. If a line is operating at full efficiency but still cannot meet demand, it may be time to consider expanding capacity or investing in faster, more advanced equipment.
- Competitive Advantage: In highly competitive markets, operational efficiency can be a significant differentiator. Companies that efficiently manage their production processes often enjoy lower production costs and faster production times, which can be crucial for winning business and enhancing customer satisfaction.
- Environmental Impact: Efficient production lines typically use less energy and generate less waste, contributing to a smaller environmental footprint. In an era where sustainability is increasingly important, improving efficiency can also improve a company's ecological compliance and public image.
Key Formula for Calculating Production Line Efficiency
The basic formula for calculating production line efficiency is:
Efficiency (%) = (Actual Output / Maximum Potential Output) × 100
This formula helps determine how effectively a production line is operating relative to its optimal capacity. Actual output is the real amount of production completed, while maximum potential output is the highest production achievable under ideal conditions.
So for example, a shoe manufacturer has an actual output of 100 shoes per day, and a maximum potential output of 120 shoes per day. Their production line efficiency would be:
(100 / 120) x 100 = 83%
Step-by-Step Guide to Using Efficiency Formulas
To effectively apply the production efficiency formula, follow these detailed steps:
- Determine Actual Output: Collect data on the actual number of units produced over a specific period. This might involve manual counting or automated data collection through production management software.
- Identify Maximum Potential Output: Estimate the ideal production volume if all conditions were perfect, including no machine downtime, no supply delays, and optimal worker performance.
- Calculate Efficiency: Use the collected data in the efficiency formula to determine the percentage of actual production relative to the potential production. This calculation provides a clear metric to assess how well the production line is performing.
One of the most reliable and cost effective ways of measuring production line efficiency is by using a manufacturing analytics software. Instead of wasting hundreds of hours manually measuring, identifying and analysing the causes of reduced efficiency, a software can do it all for you instantly.
Our product Busroot enables real-time monitoring and analysis of production metrics, providing a comprehensive overview of manufacturing operations. By integrating with existing hardware and data systems, Busroot collects and processes data from various stages of the production line, offering insights into performance bottlenecks, operational inefficiencies, and potential areas for improvement. This detailed analysis helps manufacturers identify trends, predict potential issues before they arise, and make data-driven decisions to optimise production processes.
And you can currently implement it completely FREE of cost, thanks to innovative funding from Innovate UK. Check out our Lighthouse Project page for more information!
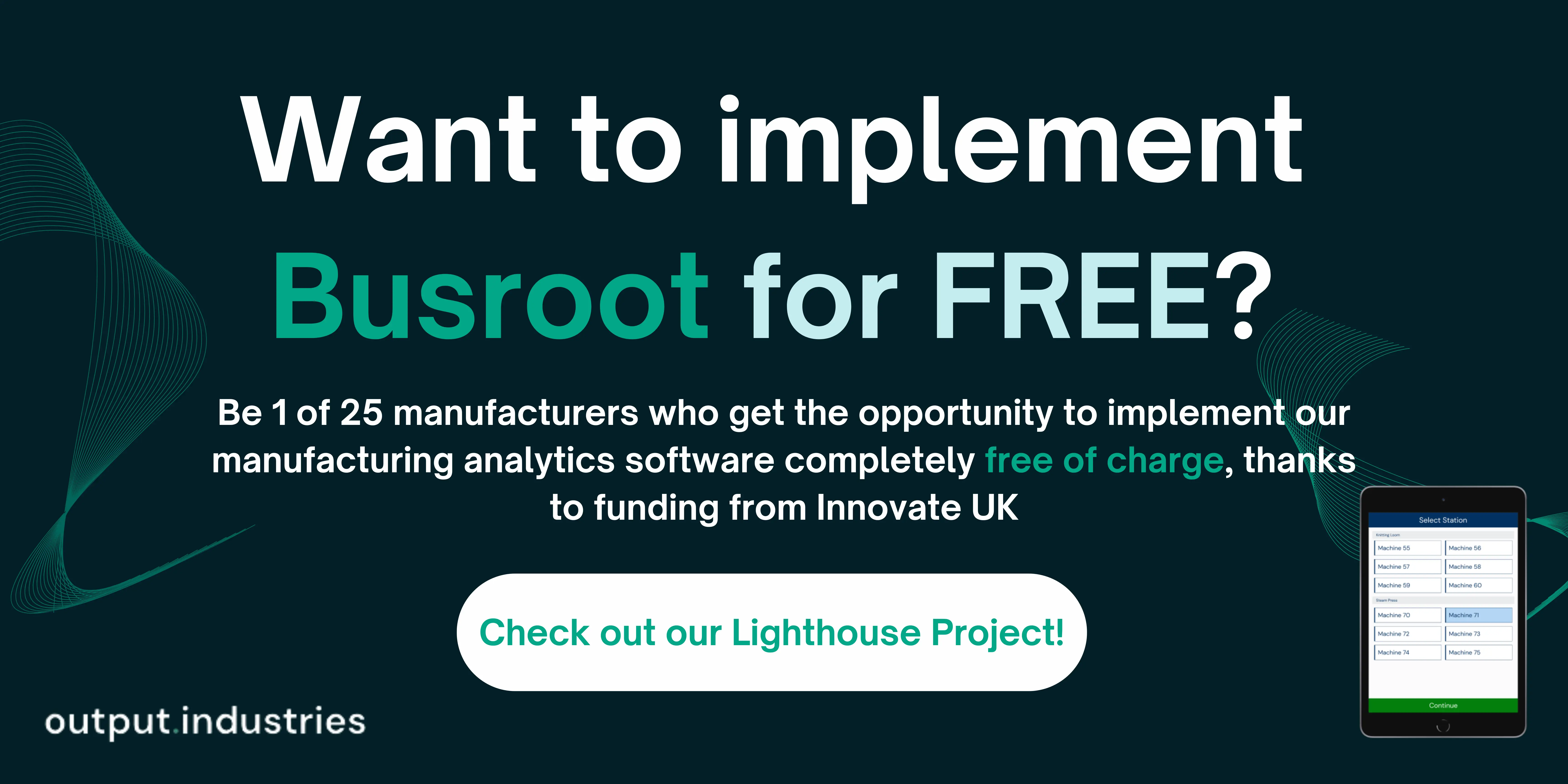
How to Interpret Production Line Efficiency Results
Manufacturers can leverage manufacturing analytics software to not only measure but also understand the intricacies of production line efficiency. Busroot facilitates this by providing detailed analytics that go beyond simple efficiency percentages to offer insights into the underlying factors affecting these figures.
Interpreting the results generated by Busroot involves a comprehensive analysis of the data to understand where and why inefficiencies occur. For instance, if the software consistently reports efficiency percentages below industry benchmarks, this could highlight several potential issues:
- Machinery: It may indicate that machines are outdated, malfunctioning, or not suitable for the required tasks. Busroot can help pinpoint which machines are underperforming and suggest maintenance or replacement schedules.
- Labour Skills: Low efficiency might be due to workforce training gaps. The software can identify production stages that frequently underperform due to operator error or slow processing times, suggesting areas where staff training could enhance performance.
- Process Design: Sometimes, the workflow or layout of the production line itself causes inefficiencies. Busroot can model different scenarios to optimise the process flow, reducing bottlenecks and improving overall throughput.
On the other hand, an efficiency close to 100% might suggest that a production line is running smoothly, but it could also indicate under-utilised capacity. This scenario might signal an opportunity to increase production loads or expand the line, thus growing output without sacrificing quality. It’s essential to compare high efficiency with industry capacity standards to determine if an increase in production is feasible and beneficial.
Busroot's ability to break down efficiency metrics by different time frames, shifts, or individual production units provides managers with the granularity needed to make informed decisions. By reviewing trends over time, managers can forecast when efficiency might dip, such as during high-demand periods, and preemptively adjust resources or processes to mitigate potential issues.
Common Challenges and Solutions in Enhancing Production Line Efficiency
Enhancing production efficiency involves overcoming several common challenges. Here are four typical obstacles manufacturers face, along with strategies to address them:
- Identifying and Addressing Bottlenecks
- Challenge: Bottlenecks can occur at any stage of the production process and are often hard to detect until they cause significant disruptions.
- Solution: Manufacturers can use tools like process mapping and data analytics to identify stages where production slows down. Solutions may include reconfiguring production layouts, automating manual processes, or upgrading machinery that causes delays. Regular analysis of production data helps in timely detection and resolution of these bottlenecks.
- Balancing Quality and Speed
- Challenge: Increasing production speed often leads to a decline in product quality, as faster speeds can result in rushed work and errors.
- Solution: To maintain both high quality and speed, it's crucial to optimise processes through quality control systems and by training employees to work efficiently under quicker conditions. Implementing technologies such as automated inspection and real-time monitoring can help maintain quality standards while improving speed.
- Managing Workforce Efficiency
- Challenge: A skilled but inefficient workforce can significantly hamper production efficiency. This may stem from a lack of training, motivation, or alignment with company goals.
- Solution: Regular training and upskilling of the workforce ensure that employees are competent and proficient in their roles. Additionally, fostering a positive workplace culture and aligning individual performance with company objectives can enhance motivation and efficiency. Performance incentives can also be effective.
- Equipment Maintenance and Upgrades
- Challenge: Outdated or poorly maintained equipment can decrease production efficiency, causing frequent downtime and higher maintenance costs.
- Solution: Implementing a preventive maintenance schedule ensures that equipment operates at optimal efficiency and minimises unplanned downtimes. When equipment becomes too outdated, investing in new technology can be more cost-effective in the long run. Upgrading to more efficient machines not only improves production capacity but also reduces energy consumption.
These detailed insights and strategies can help any manufacturing operation increase its production line efficiency, fostering better performance and profitability. If you'd like to see Busroot in action, schedule a demo with us now!