If you've reached our blog, you are probably aware of the many benefits that CNC machine monitoring software can bring to your business. CNC machines have revolutionised and automated many parts of the manufacturing process, and monitoring software further improves the efficiency and productivity of these amazing machines.
But with a fair amount of options on the market, it can be difficult to know which software is best, and which you should invest in. This blog post is going to help with all the questions you have regarding choosing CNC machine monitoring software, from how to assess your business goals, to key features to look out for.
Pre-Analysis Business Review
Before you assess any CNC machine monitoring softwares, you need to identify what you want out of the software. In order to do this, you need to assess what's currently going wrong. Are your CNC machines frequently breaking down, and you don't know why? Are your machines just not performing at their peak productivity rate? Are your machines consistently producing goods that are poor quality and cannot be sold?
CNC machine monitoring softwares often perform better in certain areas, so in order to know which one is right for you, you need to work out your primary goals. If you've identified that you are experiencing frequent unplanned stops and you aren't sure why, then you need to find a software that has exceptional downtime tracking and identification.
Similarly, if you've identified that your main issue is poor quality, then you need to find a software that excels in quality control. If you aren't sure on what questions to ask yourself, here are several questions that you can assess which will help to identify your key issues:
- Are we aware of our current production rate, and how it compares to the expected or optimal rate? If your answer is no, you need OEE tracking
- Are we aware of any noticeable patterns or trends in machine downtime or underperformance? If your answer is no, you need downtime tracking
- Do we know why the quality of our products is subpar? If your answer is no, you need a system with excellent quality monitoring
- Do we have a solid proactive maintenance schedule in place, as opposed to acting reactively? If your answer is no, you need a system that offers proactive maintenance schedules
- Are there any inefficiencies in our workflows that could be impacting the production rate? If you are unsure, you need work order management.
- Is there a system in place that notifies the correct people of an issue? If your answer is no, you need real-time alerts and notifications
- Is there a system in place for collecting and acting on feedback from the production floor? If your answer is no, you need a system that allows your employees to submit feedback
- Do we have a process in place for continuous improvement of our CNC machines? If your answer is no, you need a system that can highlight key issues and offer improvements
By answering the above questions, you can highlight key features to look for in your search.
Key Features of CNC Machine Monitoring Software
Your business review will highlight some of the features that you need to prioritise in order to chose the best CNC machine monitoring software for you. However, there are also some standard features that we believe every software should have, in order to provide people with good value for money.
Real-Time Monitoring and Alerts
Real-time monitoring and alerts are crucial for maintaining high levels of operational efficiency. The best CNC machine monitoring software offers live tracking of all machine activities, including current status, performance metrics such as OEE, and operational anomalies. You should be able to see a map of your entire shop-floor so that at any time, you can see which machines are working and which are not.
You also need to ensure the system provides immediate identification of any issues that could lead to downtime or reduced productivity. Instant alerts notify the relevant personnel to take swift corrective actions, minimising idle time and ensuring that production targets are met consistently. CNC machines have a lot of code so being able to identify the exact issue instantly and alerting the right person ensures that decision-makers can react promptly to any situation, keeping operations smooth and efficient.
Comprehensive Analytics and Reporting
Comprehensive analytics and reporting capabilities are essential for understanding and optimising manufacturing processes. A robust CNC monitoring solution will offer deep insights into machine performance, utilisation rates, and production quality. It should allow for the analysis of historical data to identify trends, patterns, and potential areas for improvement.
Customisable reports are vital, enabling users to focus on metrics that matter most to their specific operational goals. This feature supports strategic decision-making by providing a data-driven basis for enhancements, investments, and operational adjustments.
Predictive Maintenance Capabilities
Predictive maintenance capabilities are another key feature that you should look for within your CNC machine monitoring software. Unplanned stops due to machine failures are on of the biggest causes of machine downtime, and a lot of the time this could be avoided by proper maintenance activities. By leveraging machine learning algorithms and historical performance data, the software can forecast potential machine failures and suggest a plan to prevent this from occurring.
This predictive insight allows for the scheduling of maintenance activities, turning you from reactive to proactive. It also schedules maintenance during non-peak hours, ensuring machines are always in optimal condition and reducing the risk of unexpected breakdowns. Implementing predictive maintenance leads to longer machine lifespans, lower repair costs, and higher overall equipment effectiveness (OEE). As such, it's an essential feature that you should look for when choosing a software for your business.
Integration with Existing Systems
Integration with existing systems is critical for achieving a seamless operational workflow. Effective CNC machine monitoring software should be able to integrate effortlessly with other systems in the manufacturing environment, such as ERP, SCM, and CRM platforms. There's no point having a large data set if you can't feed this into your other system and make further operational gains.
The integration ensures that data collected from the CNC machines enriches the broader business ecosystem, facilitating better resource planning, inventory management, and customer service. A seamless data flow between systems enhances transparency, improves accuracy in forecasting, and supports a more agile manufacturing operation.
User-Friendly Interface and Accessibility
A user-friendly interface and easily accessible system is vital for ensuring that all team members can efficiently use the monitoring software. Employee buy-in is critical to a successful system implementation, so you need to ensure that the software you chose does not require a steep learning curve. The interface should be intuitive, easy to function, and should enable users to quickly access the information they need.
Accessibility features, such as mobile/tablet access or cloud-based operation, are also very important. You don't want your system functioning on one computer, with no flexibility or access outside of the factory. Allowing managers and operators to monitor and control production processes remotely ensures that decision-makers have the ability to oversee operations at any time and from any location, enhancing the flexibility and responsiveness of the manufacturing process.
These features not only ensure that you are getting the most value for your money but also position your manufacturing operations for improved efficiency, reduced costs, and enhanced decision-making capabilities.
Comparing different CNC Machine Monitoring Softwares
Now that you are aware of the key features you need to look for, it's time to dig in and assess the different softwares on the market. Using the following criteria will help to guide you in your comparison:
- Feature Set: Compare the features of each software to ensure they meet your specific needs, focusing on real-time monitoring, analytics, reporting, and alerting capabilities.
- Integration Ease: Assess how easily each software integrates with your existing systems and machinery. The ideal software should require minimal changes to your current setup.
- Customer Reviews and Case Studies: Look for reviews and case studies from businesses similar to yours. This can provide valuable insights into the software's effectiveness and customer satisfaction.
- Cost vs. Value: Evaluate the cost of each option against the value it provides. Consider both the initial investment and potential savings or gains in efficiency and productivity.
- Trial and Demos: Whenever possible, take advantage of free trials or demos to test the software in your environment. This hands-on experience can be invaluable in making a final decision.
Busroot by Output Industries
Busroot by Output Industries is the perfect CNC machine monitoring software for your business. It incorporates all of the features mentioned above, including OEE tracking, real-time production monitoring and alerts, downtime tracking, reporting and analytics, work order management, an intuitive interface, easy integration with existing softwares and predictive maintenance schedules.
Busroot stands out from other softwares due to it's extremely accurate data capture and use of historical data. Most CNC machine monitoring softwares attach IoT devices around but not directly touching your machines. They then register signals which infer that the machine is working. These signals can easily be mistaken though. Busroot is attached directly to your machines, uses production signals to guarantee that your machines are working, which leads to much more accurate data.
We also offer competitive pricing starting at only £150 per machine. As you add more machines, your costs decrease, giving you the absolute best for your money. And if that's not enough, we also offer a 4 week trial so you can see Busroot in action before you commit to a full contract.
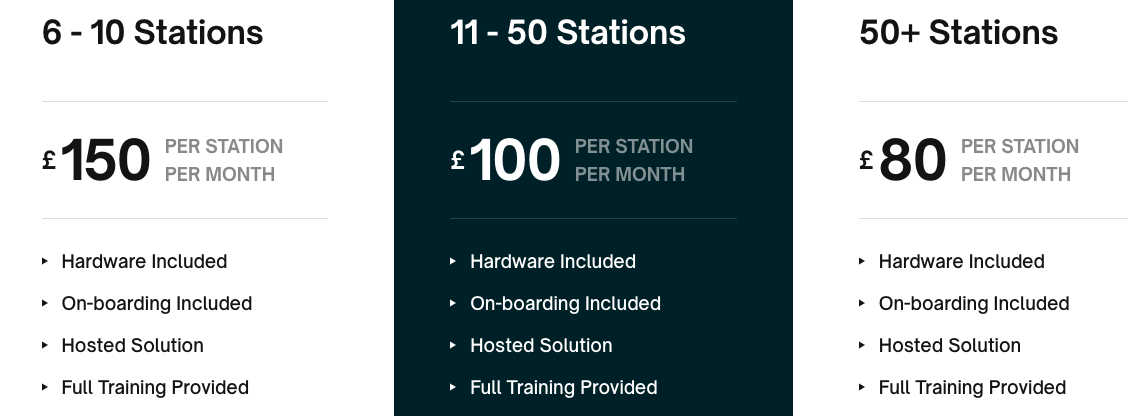
Want to see Busroot in action? Schedule a demo with us and we will show you the transformative power of our CNC machine monitoring software!