What is Production Capacity?
Production capacity is the maximum volume of products that a manufacturing setup can produce over a specified period, under normal working conditions. This measurement is crucial because it directly impacts a company’s ability to meet customer demand, manage resources effectively, and drive profitability. Understanding and optimising production capacity can lead to improved operational efficiency and a better bottom line.
What Key Factors Influence Production Capacity?
Several factors can influence a company's production capacity:
- Physical assets: The quality and availability of machinery and equipment.
- Human resources: The skills, experience, and number of operational staff.
- Technological tools: Automation and software that support production.
- Raw materials: Availability and quality of necessary inputs.
- Operational strategies: Production methodologies like Just-in-Time (JIT) or Lean manufacturing.
Types of Production Capacity
Theoretical vs. Practical Capacity
Theoretical capacity is the maximum output capability, assuming 100% efficiency with no downtime. So essentially the maximum amount of units that a factory can produce in a specific time frame.
Practical capacity refers to real-world factors affecting production. This can include maintenance, staffing fluctuations, and logistical constraints.
Peak vs. Effective Capacity
Peak capacity refers to the absolute maximum production level a plant can achieve under optimal conditions for a short period.
Effective capacity, however, is a more realistic measure that takes into account the usual disruptions and inefficiencies, representing what can consistently be achieved.
How to Calculate Production Capacity
In order to calculate production capacity, you need to follow the below steps:
1. Identify the Constraints
Begin by identifying the bottleneck in your production line, which is the slowest step that determines the maximum output rate. This could be a particular machine, a phase in the manufacturing process, or even availability of raw materials.
2. Measure Unit Production Capacity
For each machine or production line:
- Determine the cycle time: This is the time it takes to produce one unit. If a machine takes 30 seconds to produce an item, then the cycle time is 30 seconds.
- Calculate the theoretical output: This is the maximum number of units that can be produced per hour if the machine runs non-stop. For instance, if the cycle time is 30 seconds, then the theoretical output is: 3600 seconds / (30 seconds/unit) = 120
3. Adjust for Real-World Factors
Real-world production is rarely perfect, so adjust for factors such as:
- Efficiency rate: If a machine operates at 90% efficiency, then its practical output is 90% of its theoretical output.
- Downtime: Consider both planned maintenance and unplanned breakdowns. If a machine is only available for 22 hours in a day, then adjust the capacity accordingly.
For example:
Effective capacity = Theoretical Output x Efficiency Rate x Availability
If the theoretical output is 120 units/hour, the efficiency rate is 90%, and the machine runs for 22 hours, the effective daily capacity would be:
120 x 0.90 x 22 = 2376 units per day
4. Aggregate the Data
If your production involves multiple machines or lines, aggregate the capacities of all the units. Sum up the effective capacities of each machine to get the total production capacity for the plant.
5. Adjust for Product Mix
If you produce multiple products with varying demands on the machinery, calculate the capacity based on the anticipated product mix. You might need to run different scenarios to see how different mixes affect the total capacity.
6. Seasonal and Shift Adjustments
Consider how shifts and seasonal variations impact production. Adjust your capacity calculations based on different shift arrangements or seasonal workforce changes.
7. Final Calculations for Decision Making
Use these calculations to make strategic decisions, such as whether additional shifts are needed, if new machinery investments are justified, or if process improvements can enhance capacity.
This step-by-step approach will help you accurately estimate how much your production setup can deliver, which is crucial for effective production planning.
Using Software to Calculate and Monitor Production Capacity
Using tools to track and manage production capacity is one of the best ways to improve efficiency. As explained above, there’s quite a lot that goes into calculating production capacity, making it a time consuming task. Automating this by having a piece of software do it for you makes everything more straightforward.
These tools mostly come in the form of a manufacturing analytics software, which gather and analyse your production data in real time. They provide accurate and timely information, which helps you make quick adjustments to keep production lines to keep them running smoothly and efficiently.
Busroot, our manufacturing analytics software, is a great tool for managing production capacity. It fits right into your manufacturing setup using IoT devices to connect to your machines. Within a couple of hours, we can be providing insights on your production line. Over time, Busroot monitors your production capacity and alters your peak production capacity depending on
Not only does it calculate and monitor production capacity, it also monitors metrics such as OEE, machine downtime, cycle time, asset utilisation and energy usage. All this information is provided in simple dashboards, helping you to visualise your production and make timely decisions based on accurate data.
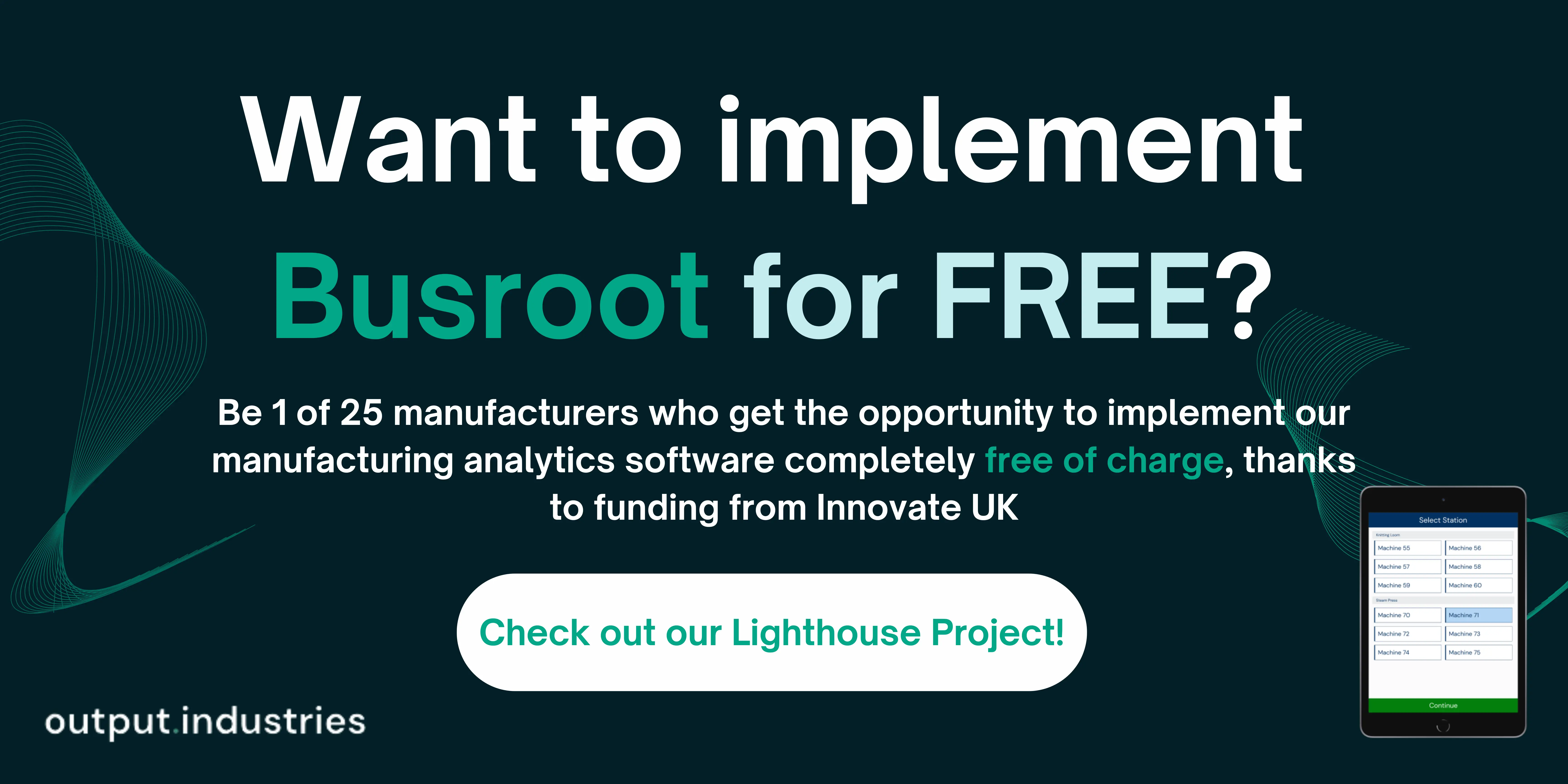
Strategies to Optimise Production Capacity
Improving Equipment Utilisation
Regular reviews and adjustments to machinery layout and operations schedules can increase how efficient you are. It reduces any unnecessary layers to your production and ensures your products are made as quickly as possible. As such, this increases throughput without the need for additional capital investment.
Leveraging Technology and Automation
Tasks that are reliant on humans are very hard to predict in terms of production capacity and are more prone to error, as there are so many factors that impact performance, such as health, concentration and skill level. Implementing technologies that can automate as many processes as possible is therefore a very good way to improve your production capacity.
Workforce Planning and Management
As mentioned previously, tasks reliant on humans have higher risk of error. Implementing flexible work shifts and cross-training employees to perform multiple tasks can therefore help in making sure your employees are happy and healthy, and can perform multiple tasks across the shop-floor.
Preventive Maintenance and Downtime Reduction
Implementing maintenance to take place just before a machine would normally break down is a great way to reduce unexpected downtime and ensure your machines are running as they should be.
Understanding and managing production capacity is vital for manufacturers to remain competitive and increase their output. Through strategic planning and the effective use of technology, businesses can optimise their operations and achieve sustained growth.