In the manufacturing industry, optimising asset utilisation is key to enhancing efficiency and profitability. By understanding how well assets are being used, manufacturers can identify areas for improvement and implement strategies to get more from their existing resources.
What is Asset Utilisation in Manufacturing?
Asset utilisation refers to the extent to which manufacturing assets (like machinery, equipment, and production lines) are used during a given period. It is an important metric because it directly impacts the output, operational costs, and overall productivity of a manufacturing plant.
Why Is Monitoring Asset Utilisation Important?
Measuring and improving asset utilsation is important because it helps manufacturers make informed decisions about the management of their equipment. Data may show that one piece of equipment is not working to it's full capacity. Operators can then investigate, identify the cause of the problem, and fix the issue. This therefore helps manufacturers to reduce machine downtime and increase production rates.
It also helps manufacturers to reduce costs. If you are constantly optimising your production processes and getting your machinery to peak utilisation, you can create more products without having to expand your facilities. It also helps to reduce the high costs associated with downtime. Finally, if you are constantly tracking your assets and logging when maintenance typically occurs, you can put in place maintenance schedules that help to reduce future downtime.
How to Calculate Asset Utilisation
Calculating asset utilisation involves several steps that take into account both the planned and unplanned downtime of equipment, as well as losses in production capacity.
- Planned Downtime: Start by determining the total hours equipment is expected to be offline for scheduled maintenance.
- Lost Operations Time: Add any additional downtime caused by factors like holidays or operational changes.
- Production Hours Lost: Factor in hours lost due to lower demand or inefficiencies.
- Unplanned Downtime: Include any unscheduled downtime from equipment breakdowns or other unexpected issues.
- Quality Losses: Convert the number of defective units into equivalent production time.
- Production Rate Losses: Assess how often equipment runs below its maximum capacity and factor this into the calculation.
Example Calculation
To illustrate, if a piece of equipment is available for 6000 hours a year but loses 1,576 hours due to downtime and other inefficiencies, the asset utilisation rate would be 74%. This means the asset is in productive use for 74% of the time.
Key Metrics to Track for Asset Utilisation
Several metrics are essential for gaining a comprehensive view of asset utilisation:
- Overall Equipment Effectiveness (OEE): This metric combines availability, performance, and quality to give an overall efficiency score. A higher OEE indicates that the equipment is running effectively without significant downtime or defects.
- Product Yield: Measures the percentage of good products produced compared to the total planned production. Low yield can highlight inefficiencies in the production process.
- Unplanned Downtime: Tracking the frequency and duration of unplanned stoppages can help identify problem areas in the maintenance and operation of equipment.
- Maintenance Spend: Monitoring how much is spent on maintenance helps determine whether it's more cost-effective to continue repairing aging equipment or to replace it.
Strategies to Improve Asset Utilisation
Improving asset utilisation involves both optimising current processes and investing in new technologies.
- Predictive Maintenance and Sensors: Implementing condition monitoring sensors can help to predict equipment failures before they happen, reducing unplanned downtime. These sensors work alongside Computerised Maintenance Management Systems (CMMS) to track and schedule maintenance more effectively.
- Optimising Plant Layout: Efficient plant layouts can significantly impact asset utilisation. For instance, ensuring that machinery is well-spaced for easy access during maintenance and operations can reduce downtime and improve safety. Clear pathways and well-organised workspaces also contribute to smoother operations and less idle time.
- Data-Driven Improvements: By implementing manufacturing analytics systems, you can track a host of metrics from asset utilisation, to OEE, to downtime. By understanding the causes of downtime, or poor quality, you can make timely decisions and improve your output. Busroot monitors all of these metrics plus energy usage and production capacity, so you will never be in the dark again regarding the status and effectiveness of your machinery.
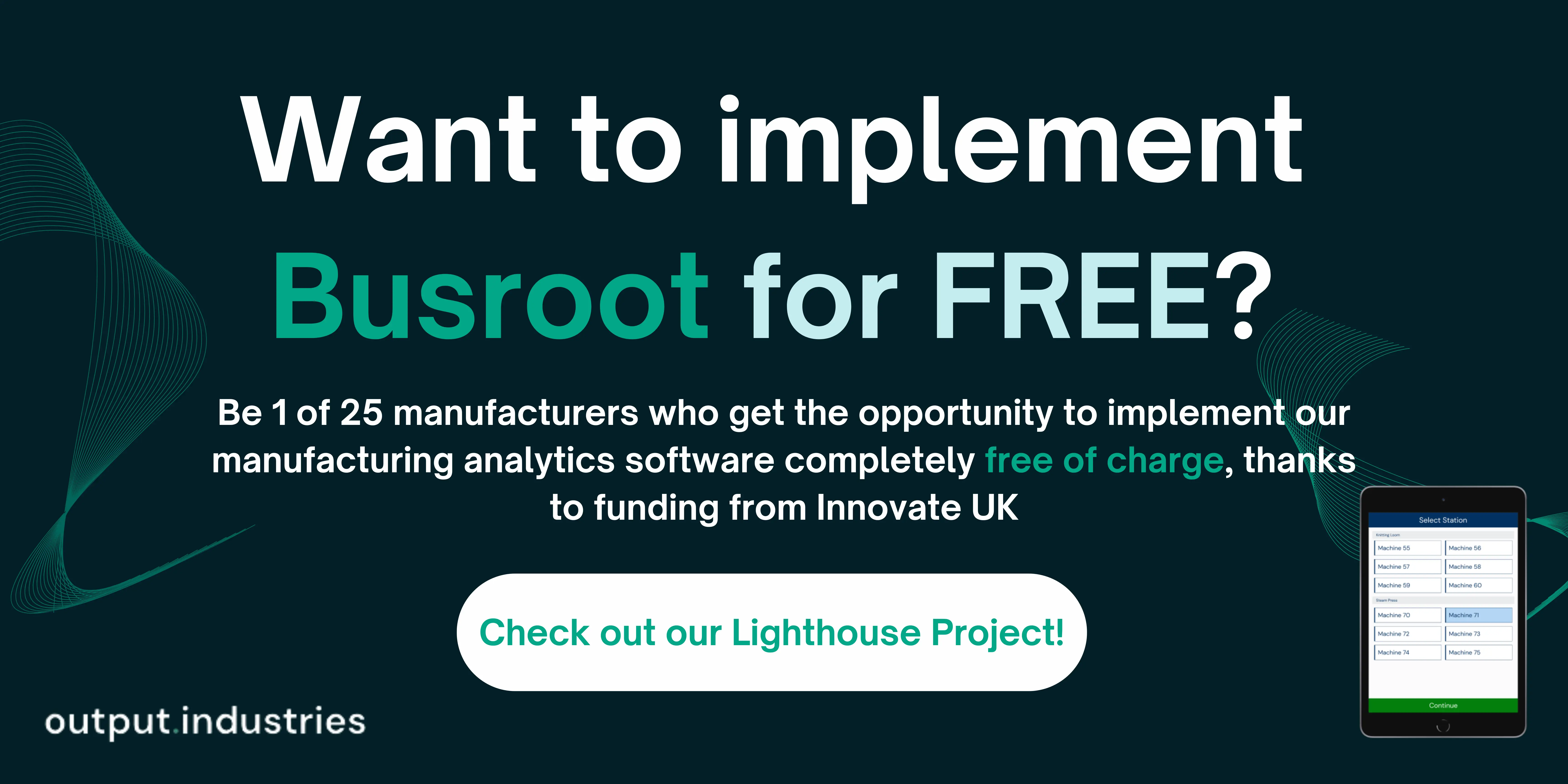
Challenges and Solutions in Asset Utilisation
Even with the best strategies, challenges in asset utilisation will arise. Common issues include equipment failures, inefficient maintenance practices, and underperforming assets. Solutions to these problems include thorough investigations of equipment failures, enhanced training for operators, and adopting a preventive maintenance strategy to minimise unplanned downtime.
Additionally, organisations should consider when to replace or reallocate underperforming assets. Decisions should be based on a combination of utilisation metrics and maintenance costs to ensure that resources are used effectively.
Final Thoughts
Improving asset utilisation in manufacturing is a continuous process that involves careful planning, monitoring, and data analysis. By focusing on key metrics and adopting proven strategies, manufacturers can maximise the efficiency of their assets, leading to better production outcomes and lower operational costs.