In manufacturing, machine monitoring involves the use of technologies and systems to track and analyse the performance of industrial machinery. It provides businesses with real-time insights into the status of their machines, and helps them to reduce downtime, enhance efficiency, and predict maintenance needs. The benefit of machine monitoring lies in its ability to transform raw data into actionable insights, ensuring that machinery operates at its optimum capacity.
Key Features of Machine Monitoring Software
Real-Time Data Collection
At the heart of effective machine monitoring is real-time data collection. IoT sensors are installed on machinery in order to continuously record a variety of parameters such as temperature, vibration, and output levels, providing a live feed of operational status.
This information is sent to a central piece of software, which then provides this information in simple dashboards for operators to oversee. At any given point, machine monitoring allows you to see the status of your shop-floor and whether you need to take any action. Without this system, problems may go unnoticed, and output will be below optimal levels.
Data Analysis and Visualisation
As mentioned, the data sent from sensors is then processed and visualised through sophisticated software platforms. These platforms provide intuitive dashboards that not only display key information, but they also measure and analyse key performance indicators (KPIs), trends, and anomalies. They can highlight when certain manufacturing metrics go below approved levels, such as OEE, machine downtime and cycle time, making it easier for managers to make informed decisions.
Alerts and Notifications
Proactive alerts and notifications is another essential feature of machine monitoring softwares. The system is programmed to warn operators and managers of deviations from normal operating conditions. This immediate feedback loop helps in taking timely corrective actions to prevent costly downtime.
You can also set up your own specific workflows. For example, an alert is sent to the operator in charge of that machine, then they must input the reason for the downtime, this is then sent to the maintenance team etc.
Integration with Existing Systems
Modern machine monitoring solutions are designed to integrate seamlessly with existing enterprise systems such as ERP and MES. This integration facilitates a unified view of operations and enhances workflow automation.
Benefits of Implementing Machine Monitoring Software
Increased Efficiency
By enabling constant surveillance of equipment performance, machine monitoring systems help in identifying inefficiencies and bottlenecks, thereby increasing overall operational efficiency.
Predictive Maintenance
One of the most significant advantages is the shift from reactive to predictive maintenance. By predicting machinery failures before they happen, companies can schedule repairs during non-operative hours, minimising impact on production.
Resource Optimisation
Efficient use of resources, including time, labour, and materials, is facilitated by detailed insights provided by monitoring systems. This leads to cost savings and reduced environmental impact.
Enhanced Decision Making
With comprehensive data at their fingertips, decision-makers can better assess risks, plan maintenance, and allocate resources. This leads to smarter and more data-driven decisions.
Types of Machine Monitoring Software
When choosing machine monitoring software, you can opt for either a cloud based or on-premise solution.
Cloud Based
Cloud based machine monitoring software involves a central system that is maintained by your provider, and accessed through the cloud. They ensure the system is working as necessary, and are responsible for any updates or maintenance. This means you do not need to install any hardware to your factory, just a simple internet connection will be enough to get you up and running.
On-Premise Machine Monitoring Software
In contrast, on-premise solutions require hardware to be installed on site, in the form of data servers and products installed onto factory computers. The system is therefore local to your factory and is maintained by you, which includes standard ongoing maintenance and any updates.
Choosing between Cloud Based and On Premise?
The choice between on-premise and cloud-based solutions depends on a number of factors such as budget, scalability, and security. Cloud-based systems offer greater flexibility and lower upfront costs, and are very scalable. However they are reliant on a stable internet connection, which may be an issue for more rural factories.
On-premise solutions might appeal to those requiring tighter control over their data and a more stable connection. However they require (sometimes expensive) hardware and a longer set up time, and maintenance is down to you, which may not be a good option for smaller businesses who don’t have a large budget.
Overall, machine monitoring is an extremely powerful activity that we’d encourage all manufacturers to implement. The real-time actionable insights provide you with a comprehensive view of your shop-floor, and allow for timely decisions to be made to improve your overall efficiency.
Want to implement machine monitoring software for free?
You could be 1 of 25 people to implement Busroot, our machine monitoring and analytics software, completely free of charge. This is made possible thanks to funding from Innovate UK, to help UK manufacturers improve their production efficiency. Check out our Lighthouse Project for more information, or get in touch now!
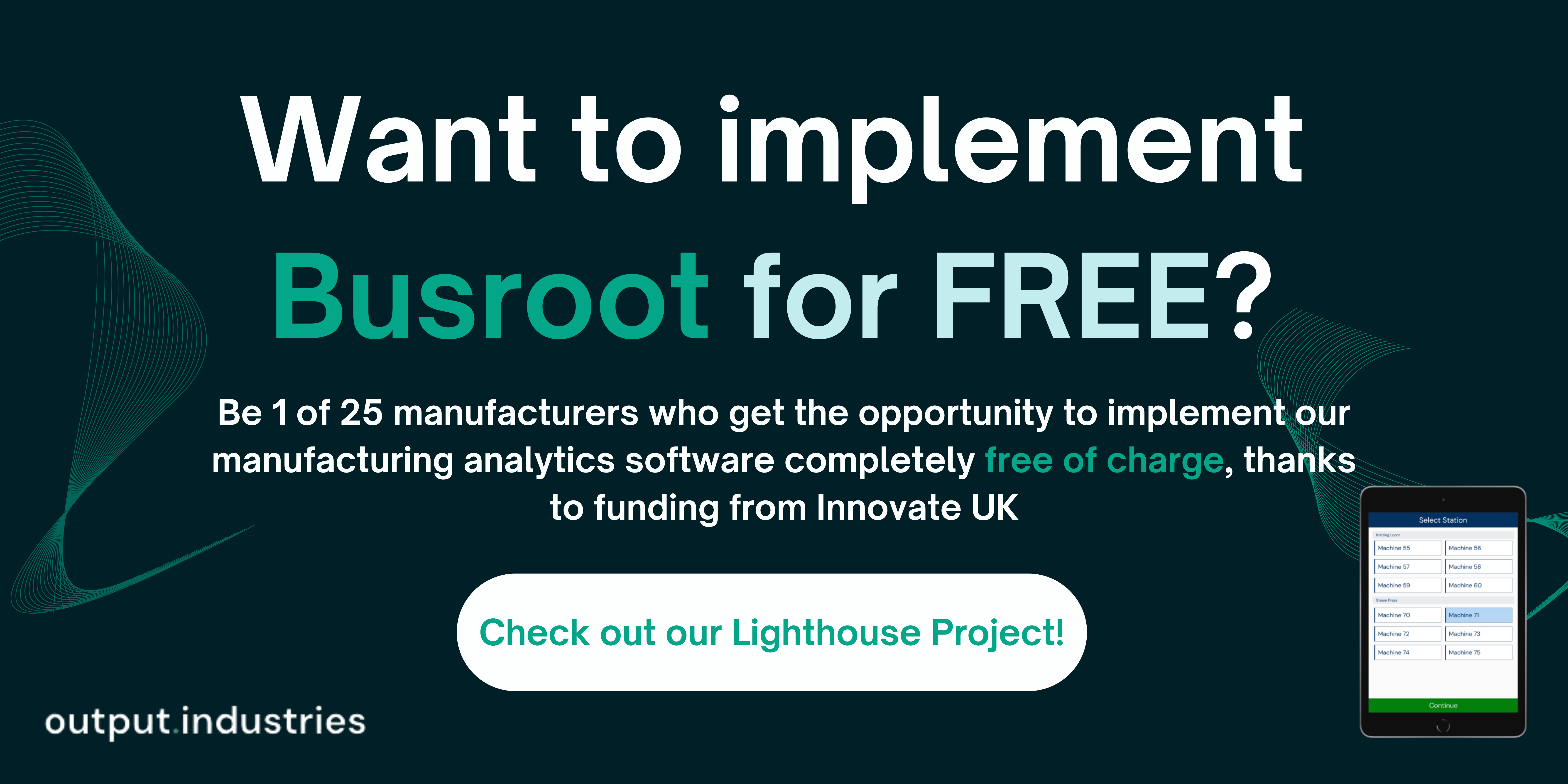