Overall Equipment Effectiveness (OEE) is one of the best and most commonly tracked metrics within manufacturing. It gives you a great oversight of how your factory is performing as a whole, but also drills down into the 3 different components (performance, availability and quality) to highlight areas that may need improving. In order to improve factory productivity/output, monitoring OEE and looking at ways to improve it as a great place to start. This blog post will give you the 10 best ways in which you can increase your OEE and improve productivity.
Invest in IoT Devices that Enable Real-Time Data Collection
Investing in IoT devices is one of the best things you can do for your organisation. IoT devices connect to your machines, enabling real-time monitoring of production performance. The devices can send updates whenever machines go down, and allow you to visualise the status of your entire shop-floor. This technology can then help in quickly identifying and addressing production issues or bottlenecks as they occur, ensuring operations remain efficient.
Our manufacturing analytics platform, Busroot, utilises IoT devices to help you monitor OEE, downtime, cycle time and asset utilisation. Not only that, but it can show you your factory's energy usage and offer ways to optimise it so you can save money. A1 Bacon implemented Busroot and saw a 14% increase in output in only 2 months!
Streamline Setup and Changeovers
Manual processes are always going to be needed within manufacturing, and unfortunately these can be the cause of significant delay. Different skill and experience levels can lead to slower changeovers and reduced efficiency. It's important to ensure every employee is carrying out the same changeover process.
Consistent repetition leads to increased confidence and less errors. By implementing techniques like SMED, you can also analyse and streamline each step of a changeover, significantly speeding up processes and enhancing productivity.
Enhance Training Programmes
Implementing frequent training programmes is another great way to improve productivity. It's understandable that people who have been doing the job for a while may fall into bad habits, such as cutting corners or not giving their 100% attention, which can impact the quality of output. Offering frequent training means that employees are always refreshed on the correct processes.
Building on that, offering training programmes that up skill your employees is a great way to improve OEE. This could include teaching employees how to spot maintenance issues, which in turn reduces downtime and improves availability.
Adopt Lean Manufacturing Principles
Lean manufacturing is all about reducing waste and improving productivity. The "6 big losses" are often referred to, and these relate to the main ways in which waste occurs in an organisation. These include:
- Equipment Failure
- Set Up and Adjustments
- Idling and Minor Stops
- Reduced Speed
- Process Defects
- Reduced Yield
By addressing these 6 factors, manufacturers can maximise their processes and improve OEE. For more on this topic, check out our blog post where we also tell you how to reduce the 6 big losses.
Carry Out Root Cause Analysis
It's so important to always carry out a root cause analysis whenever an issue arises. It's always tempting to assign the most obvious reason for a failure, but this can lead to the wrong corrective action and make the issue worse, resulting in even more downtime. Root cause analysis allows for a deeper understanding of production issues, and by identifying the fundamental causes of problems, you can implement effective solutions that prevent future occurrences.
Focus on Quality Control
Strengthening quality control processes is vital for reducing defects and reworks. Implementing frequent inspections and using statistical process control ensures high-quality outputs and reduces the cost associated with defects. This in turn, improves the quality aspect of your OEE score.
Use Predictive Maintenance
Predictive maintenance is the process of using machine learning to identify common causes and frequency of maintenance issues, and using this information to forecast potential equipment failures. This forecast can then be used to put maintenance in place that will prevent the breakdown from happening.
This is an absolutely essential part of reducing downtime and improving OEE, as it is essentially stopping the problem before it occurs. It can also help to extend the lifespan of your equipment, which can save a lot of money in the long time.
Optimise Workflow and Material Movement
Optimising workflow involves looking at your entire process and finding areas that could be streamlined. For example, you may find that the quality of your outputs is being impacted by a specific machine. By implementing a quality control station at that machine, you can send units for rework before they have wasted any further processing time, thus improving productivity.
Optimising material movement is about ensuring your inventory management is on point, ensuring you always have the perfect amount of materials in stock (not too little, not too much, just right!). This reduces production delays, increases the speed of production flow, and improves availability.
Standardise Work Procedures
Standardising work procedures ensures that all tasks are performed consistently and efficiently. Humans being humans means that people have a tendency to do things differently, so developing and enforcing standard operating procedures (SOPs) helps to maintain high performance levels across the board.
Embrace Continuous Improvement
Embracing a culture of continuous improvement is key to enhancing processes and reducing inefficiencies. Continuous improvement is always striving to improve processes, products or people in any way possible.
There are many different continuous improvement initiatives that you can implement, including Kaizen, Kanban and Six Sigma. Adopting a culture of continuous improvement also encourages all employees to contribute ideas that help in ongoing operational improvements, and this will naturally improve OEE.
By implementing all of the above techniques, you can improve your OEE and power efficiency gains for your business. Manufacturing analytics software is truly the key to improving OEE, so get in touch if you’d like to find out more!
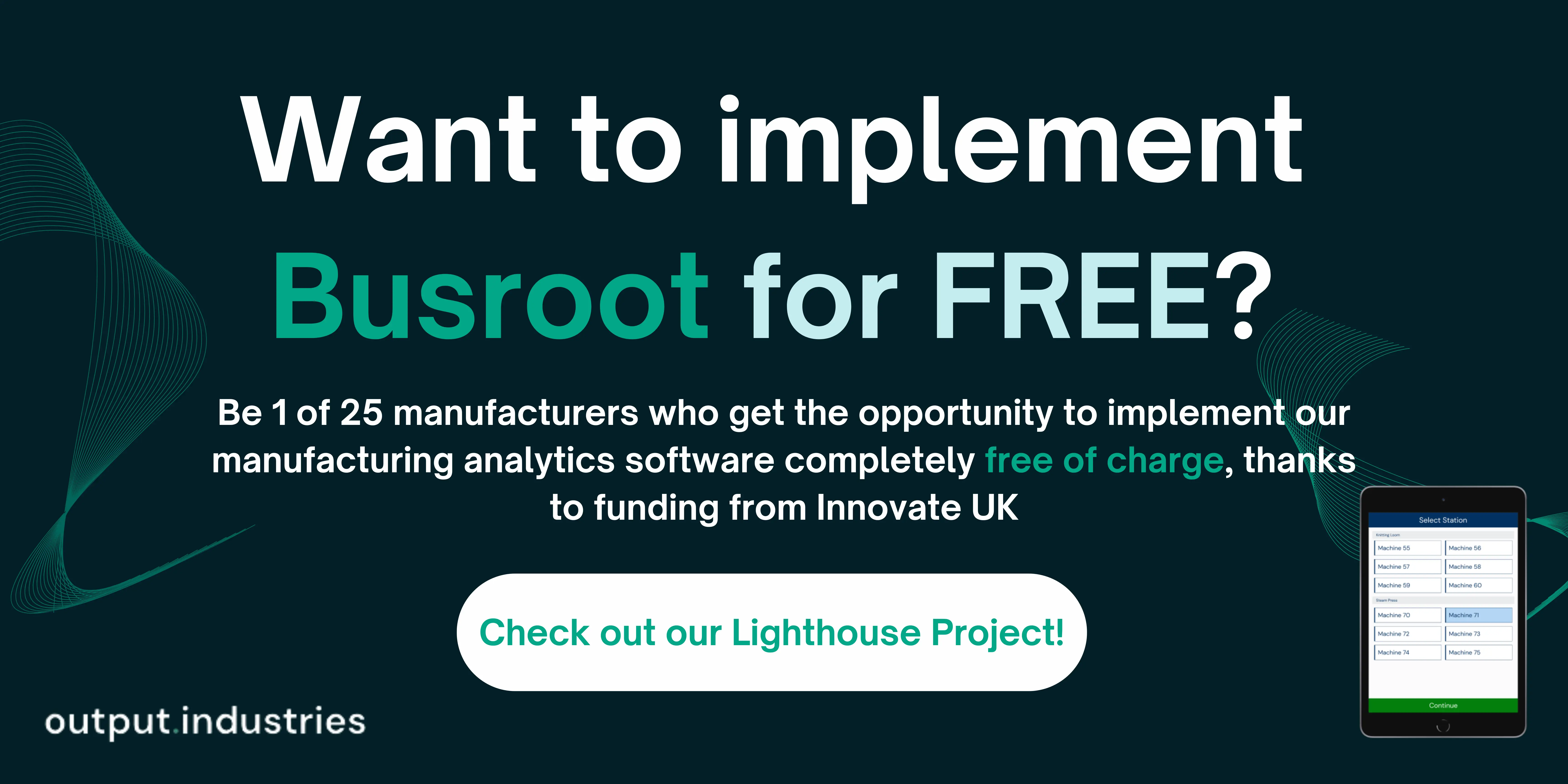