Digital transformation in manufacturing isn't just buying new machines, or automating a few processes; it’s about using technology to fundamentally change how you operate and deliver value to customers. It's involves integrating digital technology into all areas of a business, so that you can become as efficient as possible. This shift not only helps companies keep pace with emerging market demands, but also drives innovation and improvement at every level.
Essential Technologies Driving Digital Transformation
Industrial Internet of Things (IIoT)
IIoT devices have become a key component of manufacturing digital transformation. These devices connect to factory machines, which enable real-time data collection and analysis. The information from the devices is sent to a central system, which is then used to make timely and strategic decisions. For example, you may find that a machine is consistently halting production due to overheating. You make the decision to purchase cooling equipment, leading to reduced downtime and increased output. This connectivity and data can therefore become a game changer for manufacturers.
Artificial Intelligence and Machine Learning
As we've seen recently, AI and machine learning have made huge waves, and manufacturing has not been immune to this. AI is now being used in many ways, including:
- Analysing past data to identify trends and create predictive maintenance schedules
- Highlighting early patterns that may suggest an issue is present, long before humans would be able to identify the problem
- Creating complex code for CNC machines
- Supporting employees in product design and development
- Supporting website and marketing teams with product descriptions, content creation and more
All of this support helps give employees more time to work on activities that actually move the needle. This in turn can lead to higher productivity and reduced operational costs.
Cloud Computing
Cloud computing offers scalable resources and data storage solutions, providing manufacturers with flexibility and enhanced collaboration capabilities. It enables smaller manufacturers to be able to make use of advanced technology, without having to pay for expensive equipment installation and maintenance. Cloud computing supports other technologies on this list by offering a central platform for accessing and analysing data in real-time, which can often be accessed by employees wherever they are.
Modern Machinery
Modern machinery is another big component of digital transformation. Updating legacy equipment is a great way of enhancing efficiency, minimising waste, and improving product quality. Here are a few examples of modern machinery that are being increasingly implemented:
- CNC (Computer Numerical Control) machines - CNC machines automate precise cutting and milling, drastically reducing human error and accelerating production.
- Robotic automation - Robotics incorporate AI to perform complex assembly operations and real-time process optimisations, particularly evident in sectors like automotive manufacturing.
- Laser cutting - Lasers provide high precision in working with various materials, ideal for detailed designs that traditional methods cannot achieve.
- 3D printing or additive manufacturing - 3D printing offers unprecedented flexibility in design and the ability to produce complex structures directly from digital models. They can help with both prototype development and custom manufacturing, due to the ability to produce one unit on demand, as opposed to having to order batches from suppliers.
Big Data Analytics
Big data analytics combines all of the above technologies to create a piece of software that can power significant efficiency gains. Because at the end of the day, what's the point in having all of these technologies if you don't know how to use/optimise them?
Vast amounts of information from modern machinery is collected through IIoT devices, which is sent to the cloud to be analysed and broken down into actionable insights that drive informed decision-making. Manufacturers can use these insights to predict customer behaviour, streamline operations, and optimise production output.
For example, Busroot (our manufacturing analytics platform) measures all of your key manufacturing metrics including machine downtime, OEE, cycle time, asset utilisation and energy usage. It creates predictive maintenance schedules, shows you areas where you can optimise your energy usage, and highlights inefficient processes that could be improved. Essentially, data analytics software like Busroot is the key to combining all aspects of your digital transformation and creating actual change in your business.
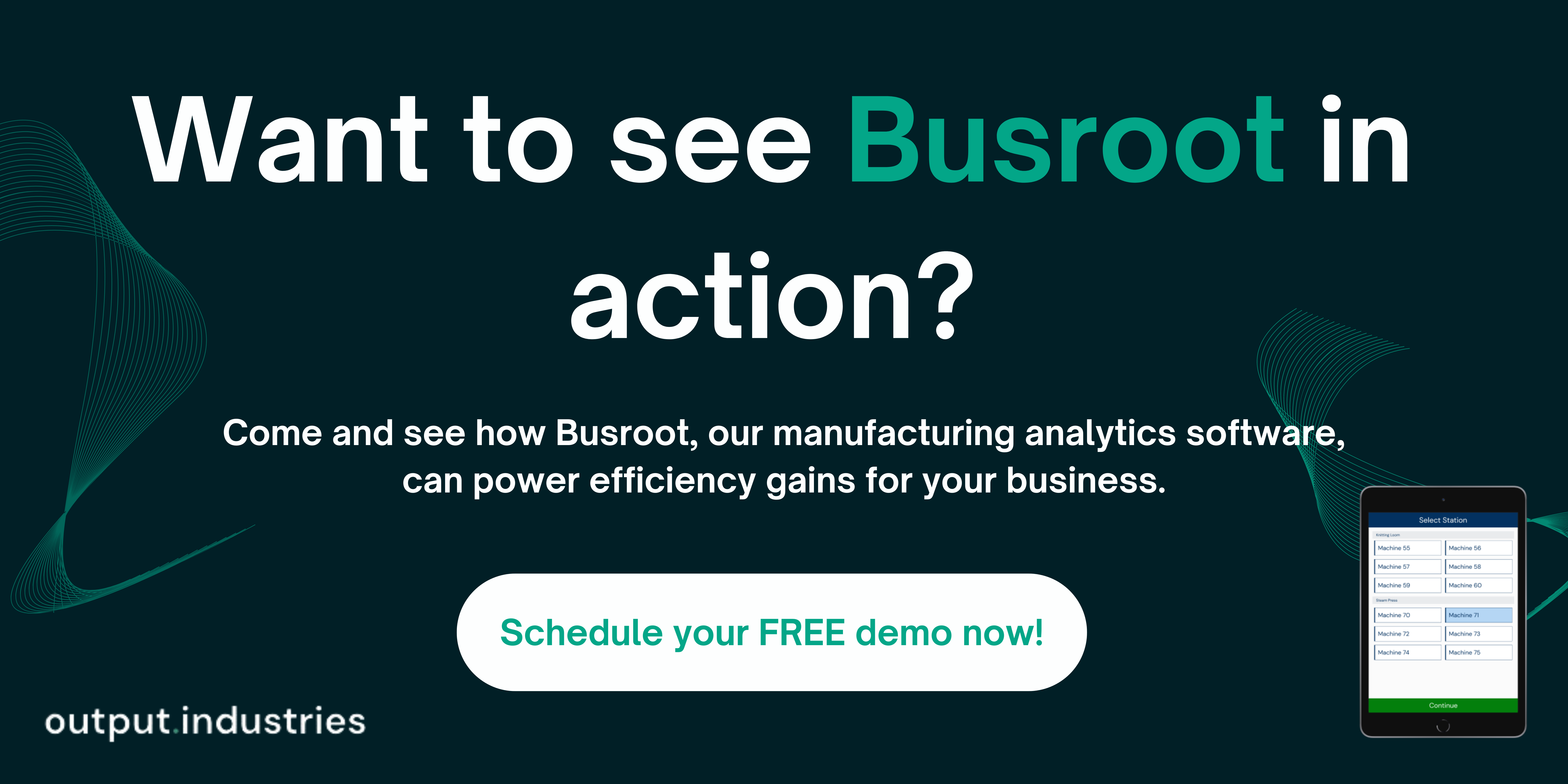
Key Benefits of Digital Transformation for Manufacturing Profits
Increased Operational Efficiency
Digital transformation significantly enhances manufacturing profits by increasing operational efficiency. Technologies such as predictive maintenance, powered by AI, foresee equipment failures and schedule timely repairs, drastically reducing costly downtime. Real-time monitoring systems keep production consistently at peak performance, quickly correcting deviations that might slow down the workflow. These efficiencies translate directly into lower operational costs and higher output, substantially boosting the bottom line.
Cost Reduction from Waste Minimisation
Digital tools directly enhance profits by cutting operational costs and reducing waste. Energy-efficient machinery and energy optimisation powered by insights from analytics software, help manufacturers to reduce their electricity consumption and utility bills. Using AI to maximise product design and materials usage can also help to decrease costs from waste, which can then lead to a reduction in waste management expenses. By streamlining these aspects, manufacturers not only save money but also enhance their profit margins significantly, providing more capital to reinvest in business growth.
Enhanced Product Quality and Customisation
By leveraging digital technologies, manufacturers can dramatically improve product quality and offer extensive customisation, directly impacting profits. High precision tools like CNC machines and robotic arms produce superior products with fewer defects, reducing costs related to rework and returns. Customisation through digital platforms like CAD and CAM meets specific customer demands, allowing manufacturers to command higher prices and improve customer satisfaction. This adaptability to customer needs not only attracts more business but also fosters customer loyalty and repeat sales.
Improved Supply Chain Management
IoT and advanced analytics provide critical visibility into every stage of the supply chain, enabling rapid responses to supply and demand changes and minimising costly delays or stockouts. Better inventory management through data analytics prevents overproduction and understocking, optimising cash flow and reducing wastage. These improvements ensure a more reliable supply chain, less capital tied up in inventory, and a smoother production line, all of which are crucial for maintaining profitability in competitive markets.
Steps for a Successful Digital Transformation in Manufacturing
Assessing Current Processes and Setting Objectives
The first step in digital transformation is to thoroughly assess existing manufacturing processes and define clear objectives for integration of digital technologies. This assessment helps pinpoint inefficiencies and areas for improvement, setting a foundation for a successful transformation strategy.
Investing in the Right Technologies
Selecting the right technologies is critical for effective digital transformation. Manufacturers must choose solutions that align with their specific needs and goals, ensuring that each technological investment drives value and enhances competitive advantage.
Training and Upskilling the Workforce
As digital tools are integrated, it’s vital that the workforce is trained and upskilled to handle new technologies. Continuous education and development programs are essential to empower employees and ensure they are proficient in the latest manufacturing technologies.
Developing a Phased Implementation Plan
Implementing digital transformation should be a phased process, with each step carefully planned and managed. This approach minimises disruption to existing operations and allows for adjustments as feedback and results are evaluated throughout the implementation.
Digital Transformation Challenges and How to Overcome Them
Implementing new technologies into your manufacturing organisation is not a small task. It requires careful planning and execution, but even with the best intentions, issues can arise. These are the most common challenges we've seen and how you can avoid them.
Cultural Resistance
One of the most common challenges in digital transformation is cultural resistance from within the organisation. Employees may be resistant to change due to uncertainty or fear of technology "taking their jobs". Overcoming this barrier involves proactive change management strategies, including clear communication about the benefits of digital transformation and involving staff in the transition process. Training and education programs can also help ease the transition, showing employees how new technologies can make their jobs easier and more secure.
High Initial Costs
The initial investment required for digital technologies can be substantial, posing a significant hurdle. To manage this challenge, manufacturers should adopt a strategic approach to investment, starting with pilot projects that require minimal upfront costs and show quick returns. This can help in securing further investment based on demonstrated ROI.
Additionally, exploring various financing options such as loans, grants, or partnerships can alleviate financial pressure and facilitate smoother adoption. We are offering 25 manufacturers the chance to implement our manufacturing analytics platform completely free of charge, so get in touch to see if you could be one of them!
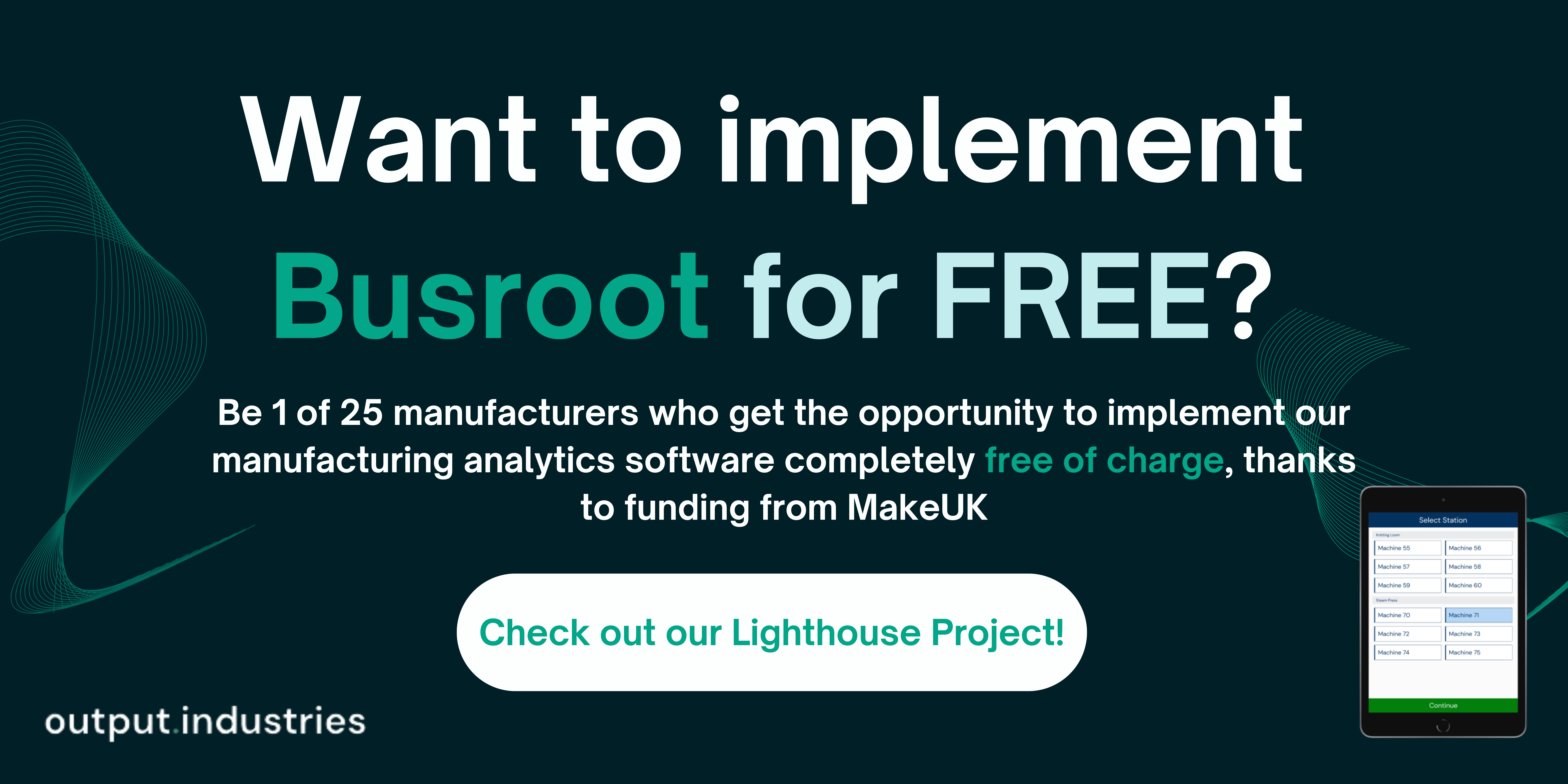
Technical Integration Issues
Integrating new digital technologies with existing IT systems such as ERP and MES can be complex and disruptive. To address these technical challenges, manufacturers should engage with experienced IT consultants who can provide guidance on seamless integration strategies. Adopting a phased approach to technology integration can also help manage complexities by allowing adjustments to be made gradually and reducing the impact on ongoing operations. Ensuring strong IT support throughout the process is crucial to address issues as they arise promptly.
Cybersecurity and Data Protection
As digital tools become more integrated into manufacturing processes, the risk of cyber threats increases. To mitigate this risk, it is essential to implement robust cybersecurity measures and data protection protocols. Investing in up-to-date security software, conducting regular security audits, and training employees on cybersecurity best practices are critical steps. Additionally, manufacturers should develop and enforce strict data access policies to protect sensitive information and maintain customer trust.
The impact of digital transformation in manufacturing cannot be understated. It offers substantial benefits including enhanced operational efficiency, cost reductions, improved product quality, and superior supply chain management, all of which significantly boosts revenue and profit margins.